Our freshwater hatchery locations
Our freshwater hatchery locations
Freshwater
Our two freshwater facilities located throughout the South Island of New Zealand collectively breed, hatch and grow smolt for our seafarms.
Breeding programme
Our classical breeding programme has been in place for more than 28 years and is the longest running, commercial selective King salmon breeding programme in the world. It delivers the critical scientific rigour to our unique breed of King salmon. The salmon we use for breeding are referred to as our ‘broodstock’.
Our breeding programme has spanned across 8 generations of salmon, with approximately 150 families and records on more than 200,000 fish.
Generations of salmon
Years established breeding programme
Families of salmon

We believe the result of this programme, which crosses the traits of observed families for beneficial inherited characteristics, is salmon with superior characteristics to that of wild King salmon. Our primary focus has been on developing salmon that are bred for culinary excellence and that grow faster, and therefore larger, than wild King salmon – in addition to having a higher fat content which is highly desirable for our discerning chefs around the world.
Freshwater process
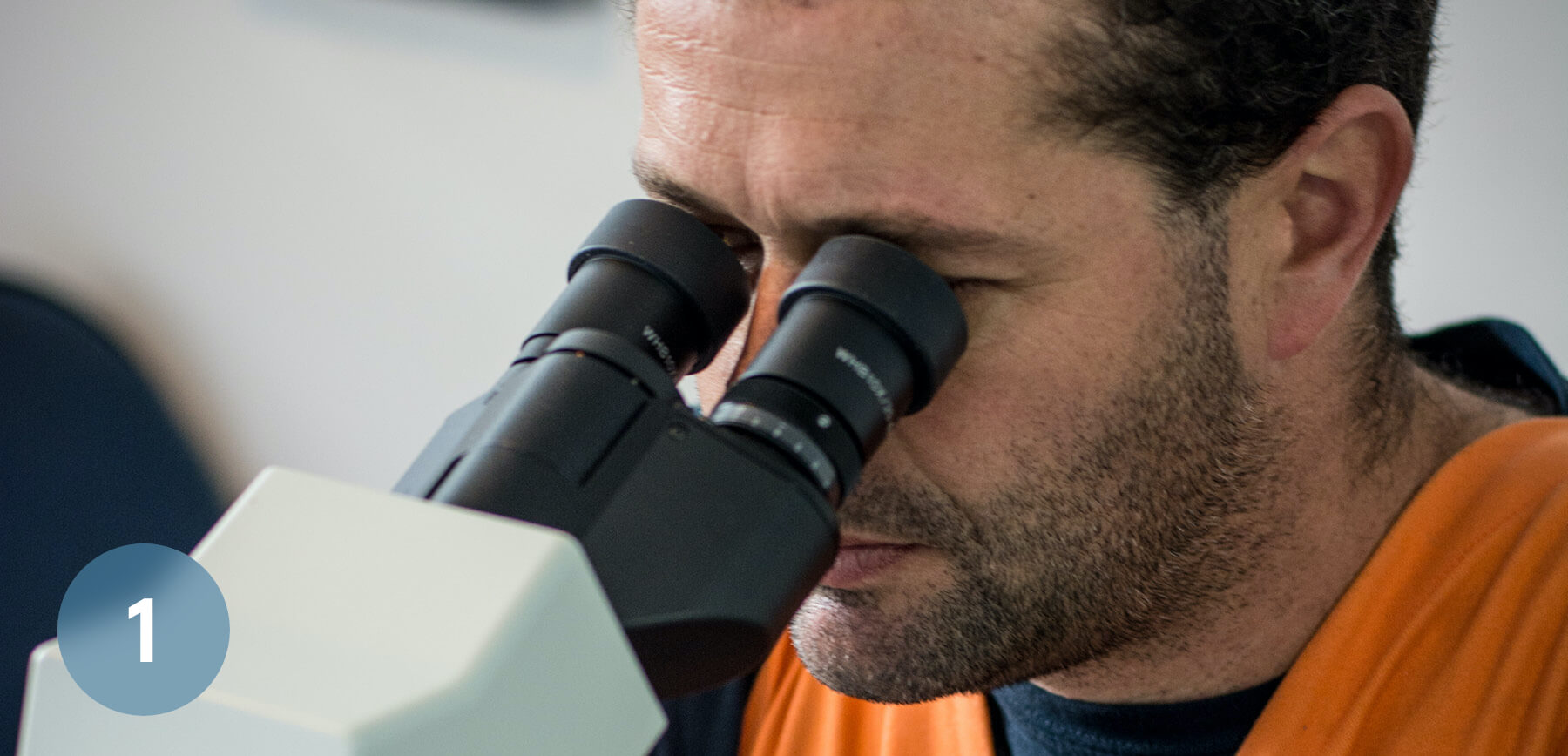

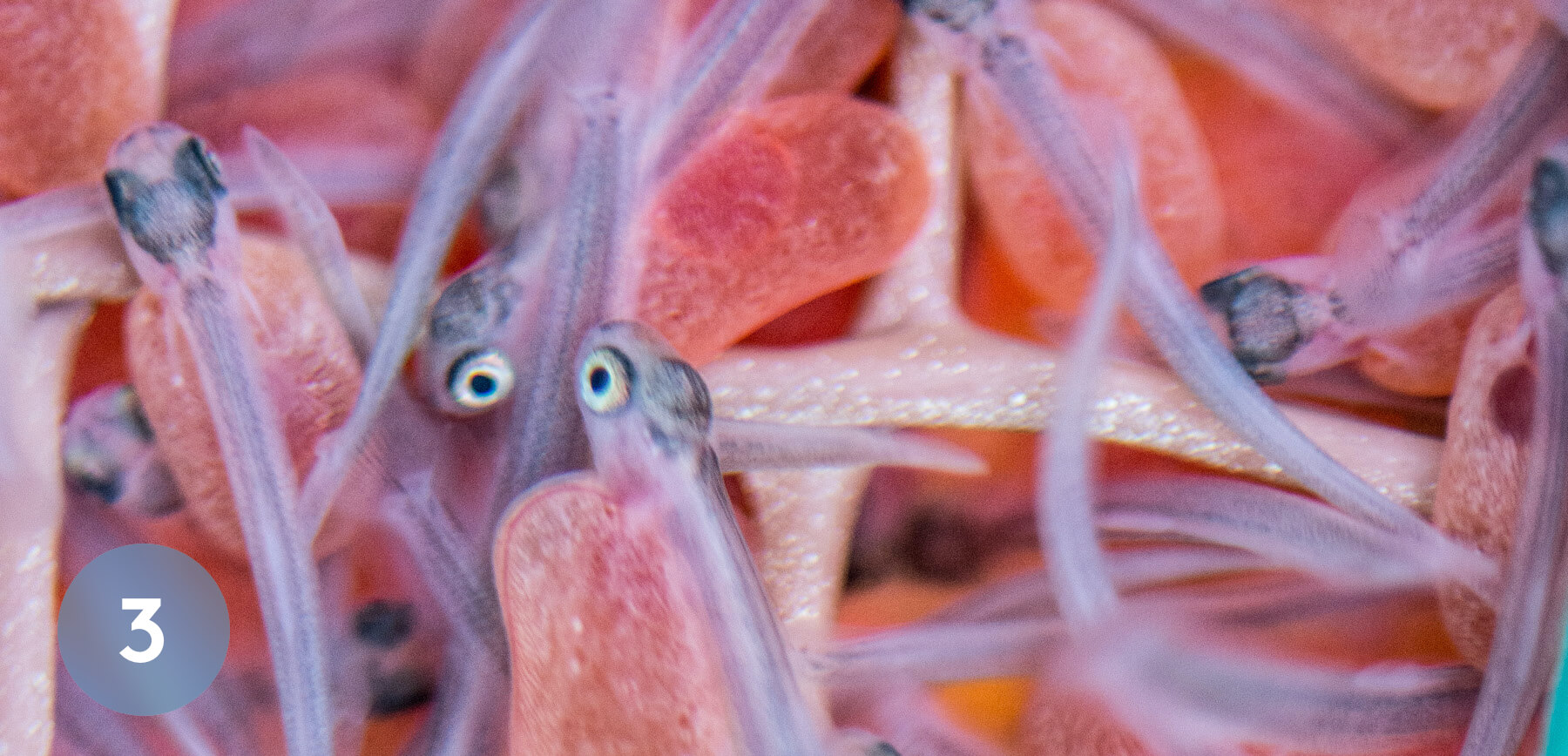
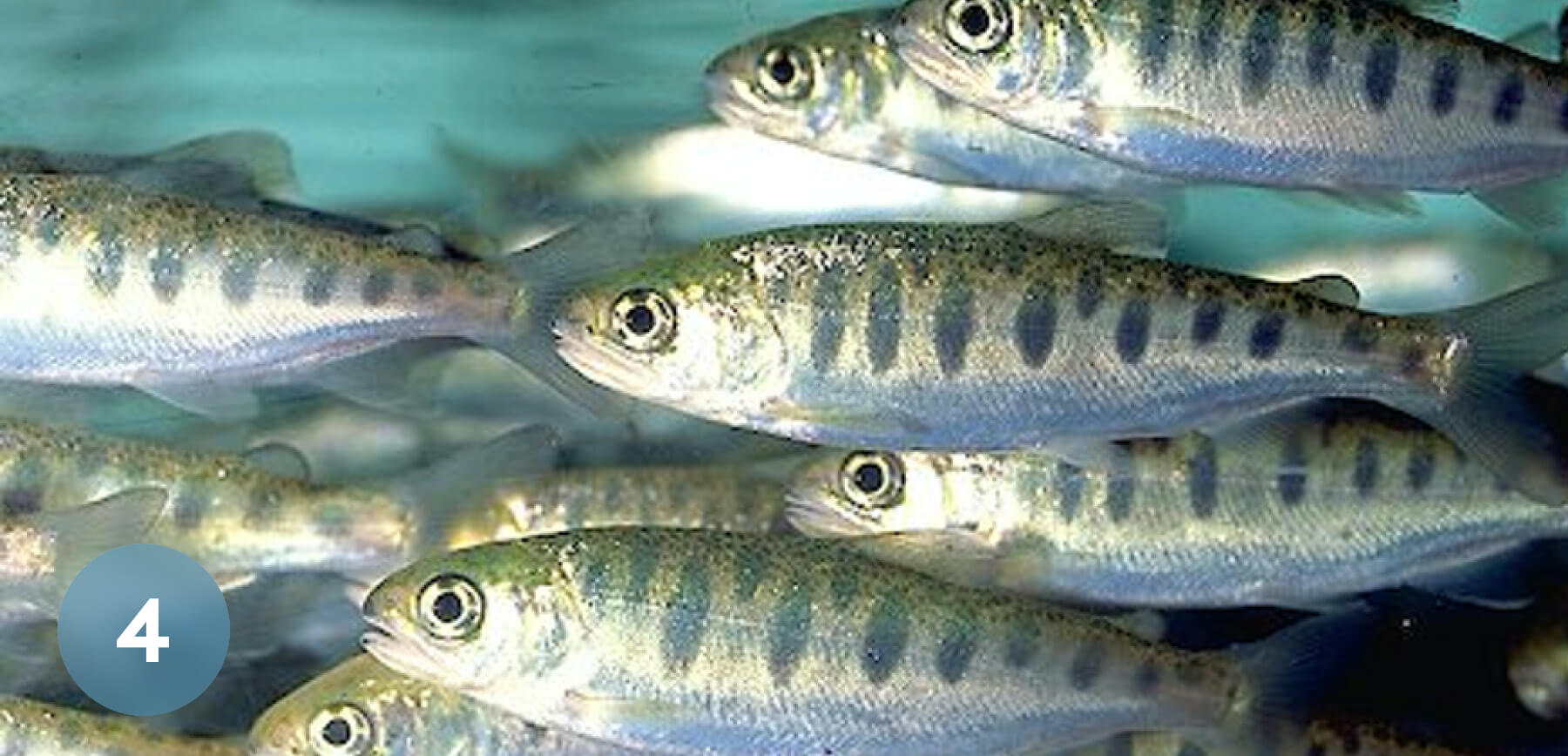
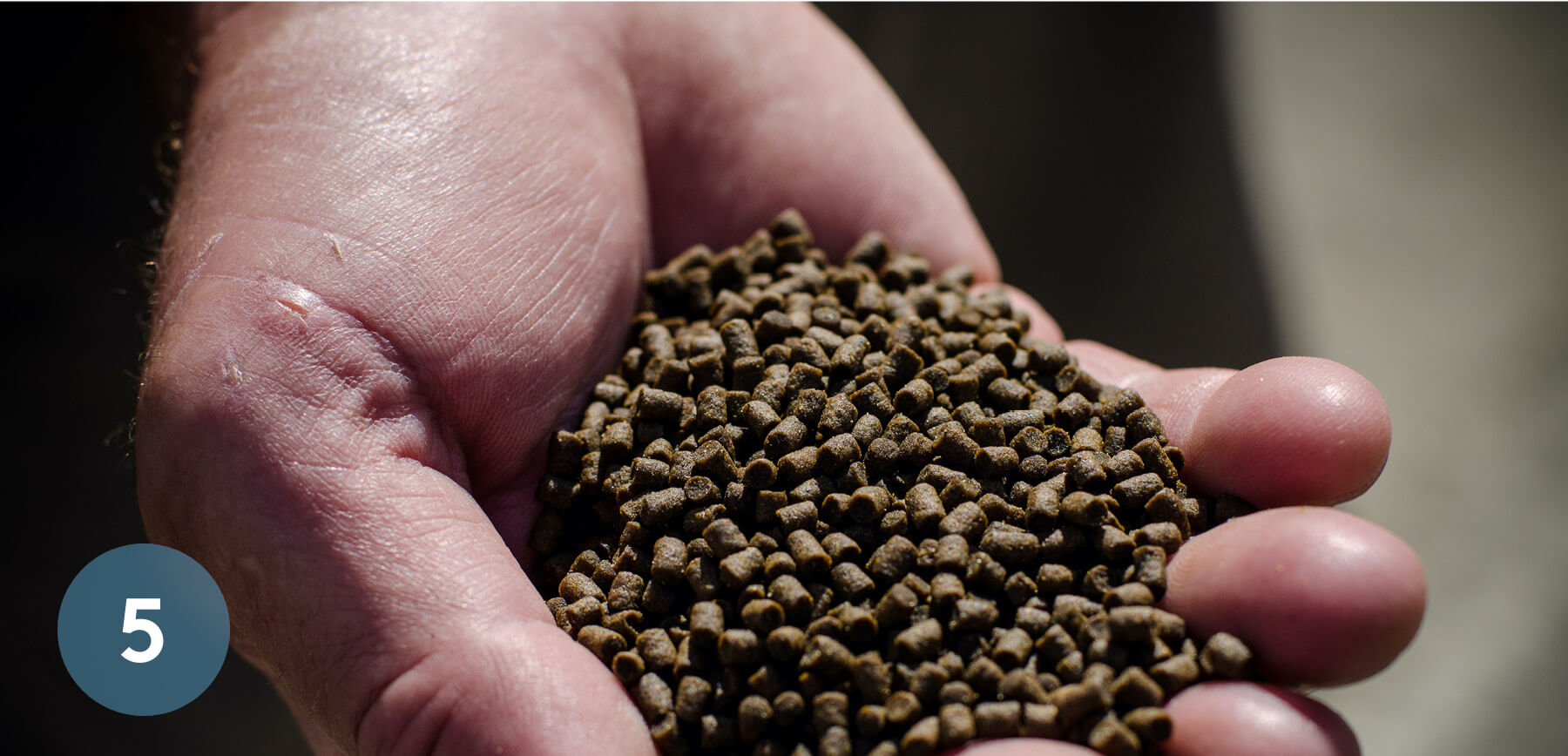
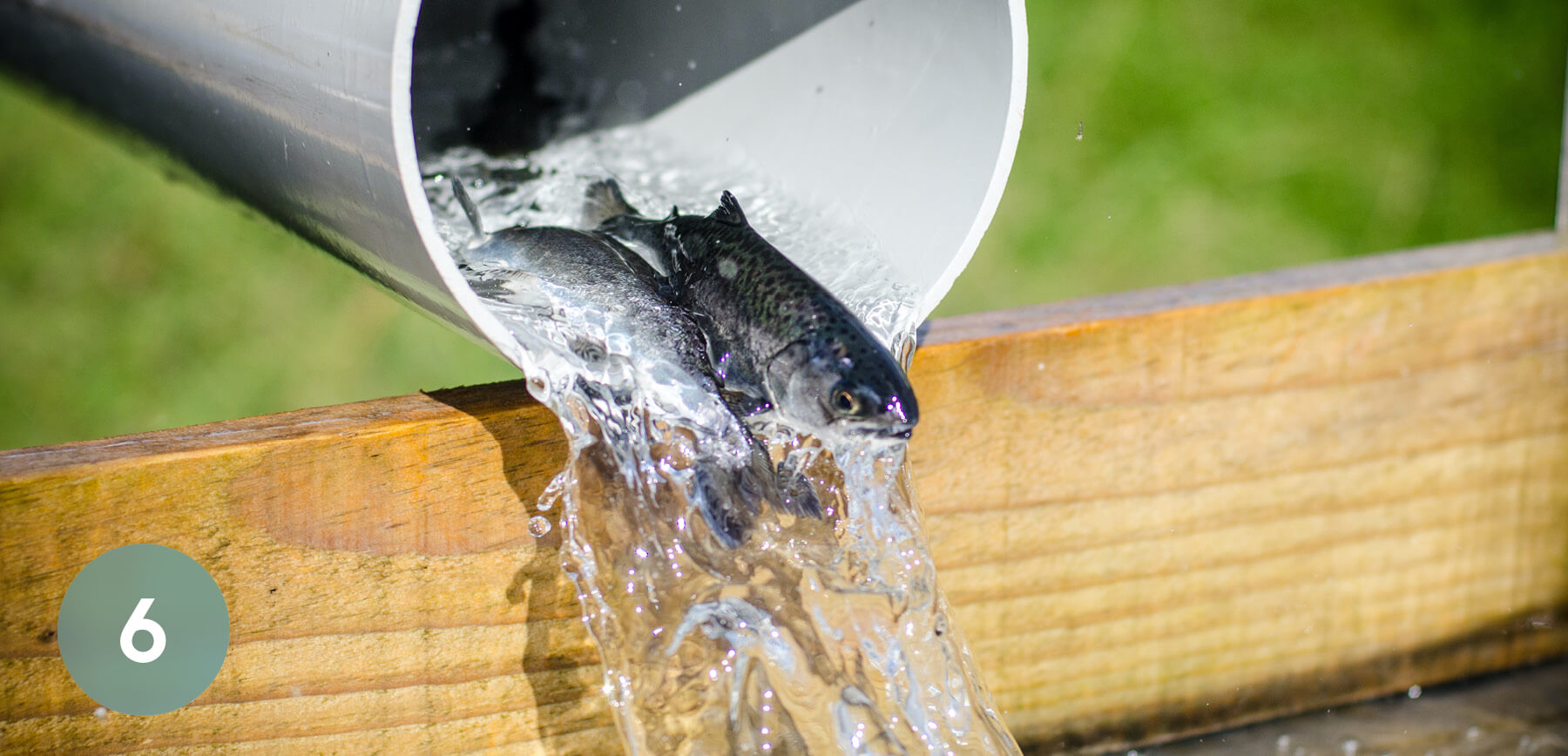
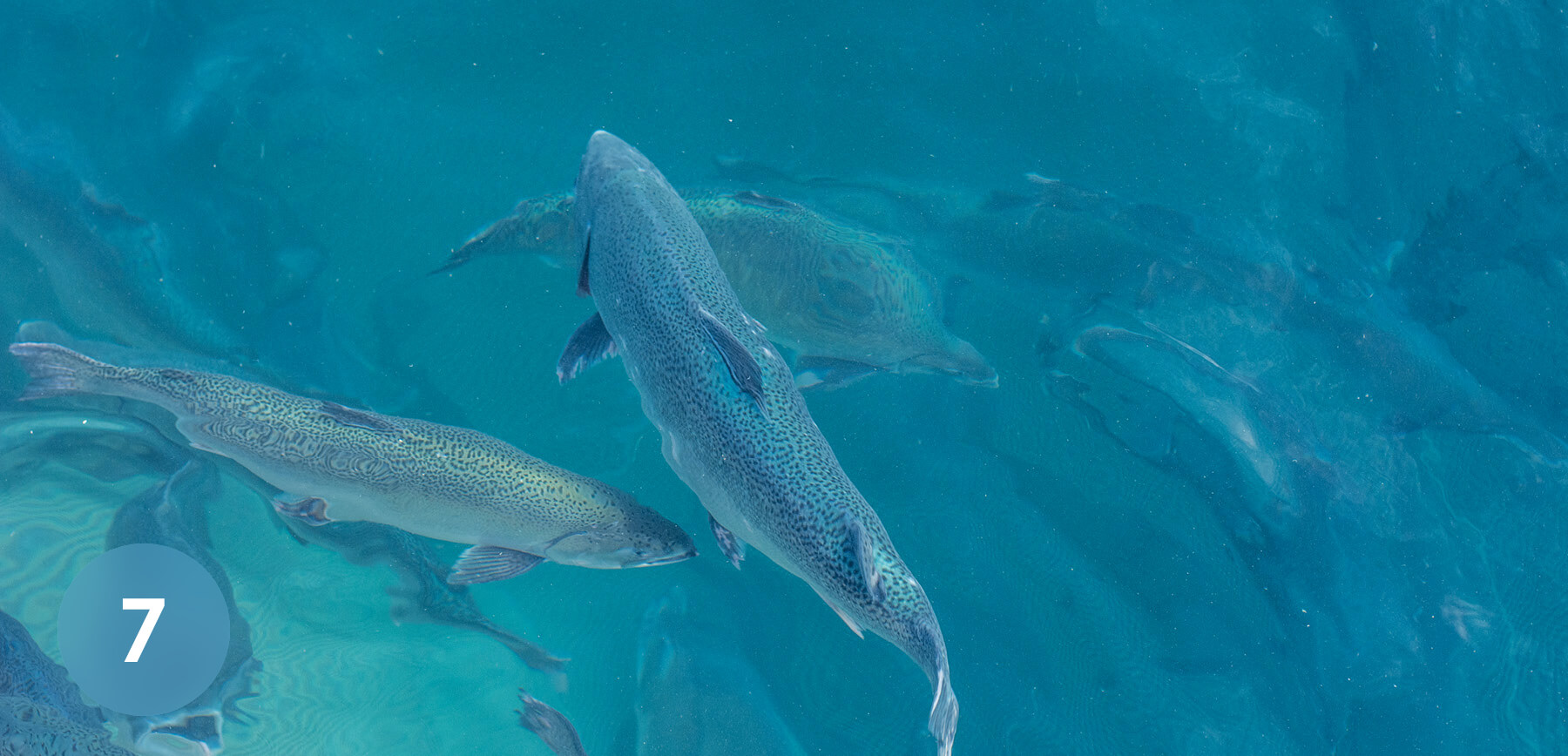
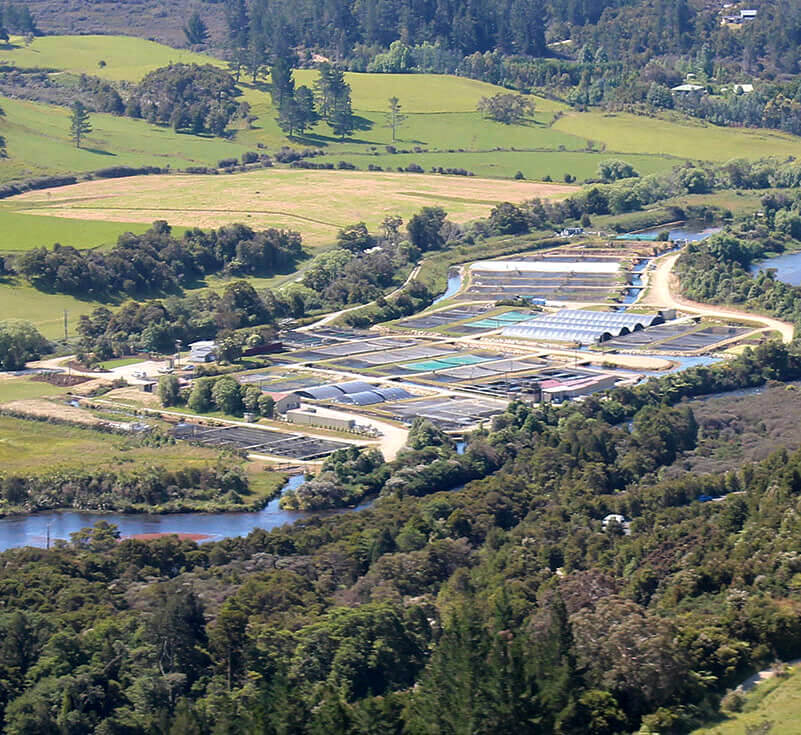
Tākaka, Golden Bay
Broodstock facility
Located immediately downstream from Te Waikoropupū Springs in Takaka, Golden Bay, this facility benefits from one of the clearest sources of fresh water in the world. Bubbling from the ground at approximately 14,000 litres / second at a relatively stable temperature of just below 12°C, it provides optimum conditions for rearing our King salmon. This site was the first commercial King salmon hatchery established in New Zealand and produces up to 7 million ova per year.
Most recently it has also become home to our world-first Ora King TYEE salmon.
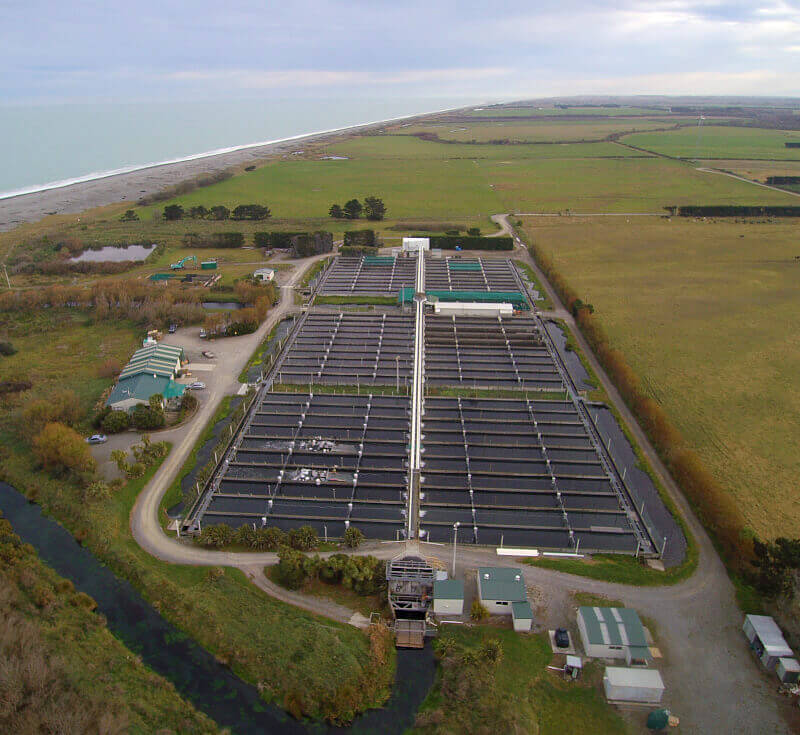
Tentburn, Canterbury
Smolt facility
Close to the mouth of the Rakaia River in Canterbury, Tentburn receives ova from our Takaka facility. Tentburn is great for producing smolt for sea pen grow-out, with the main advantages being plentiful land area, good access and suitable freshwater supply. Using technology developed in the United States, the Tentburn hatchery has 60 raceways, and water is continuously pumped from two spring fed streams. Two wells are also used at Tentburn to obtain better quality water for incubation and development of the smolt during the early stages of the lifecycle. The Tentburn facility produces over 3,000,000 smolt annually.